PTS is one of the largest suppliers of decorated tableware in the world. PTS America is the brain behind the marketing, design and distribution of its products to large-scale retailers in North America, Canada, and parts of South America. With its highly specialized team of designers, PTS America designs high quality and unique contemporary and classic tableware for its customers. Not only that, it creates and markets its products under its own brands like 222 Fifth, Coventry, and other private labels of a variety of renowned retailers.
The Context
Being in the business of decorated tableware, PTS America has amassed a huge collection tens of thousands of designs and graphic files. The PTS America team managed all of their designs in their own workstations and there was little organization as to where all the designs were kept. There was an enormous archive of design work that couldn’t be searched – no one knew where to find a design, who created it, or how to find it again. Literally millions of dollars in assets they were unable to tap into.
PTS America also was in need of a library for basic design tools and building blocks. For example, a dinner plate can have a variety of basic shapes and may come in 5 or 6 different forms from the factory. To decorate it, a graphic on a decal is printed and the decal film is put on the plate which is gloss fired at high temperature (900 – 950 C) causing the pigments printed on the film to be fused with the surface. The company often purchases graph cards from artists who creates textile or wallpaper designs (called purchased art). The purchased art is scanned and digitized so it can be customized to any shape or design that fits the tableware.
“We needed a library of factory shapes, decal templates, purchased art, fonts, logos, schematic drawings, etc. which was easily searchable. We wanted to store the designs in an organized manner so that any designer who wanted to work on them can find their way around the resources easily.” – says Charles Gallagher, Executive Vice President of PTS America.
Another major issue PTS America faced was its reliance upon email and spreadsheets to manage work and exchange large files between its designers, clients, and the factory. The company needed to automate the collaboration and tracking processes between its different departments and global locations. Manually managing this was time consuming, chaotic and left a lot of room for mistakes. This caused PTS America to run the risk of missing product delivery deadlines and inevitably lowering its customer satisfaction metrics.
So, to find a content management system that will handle all these issues, PTS America reached out to its consulting partner, StrikeTru. After a rigorous evaluation of available content management systems, StrikeTru selected Nuxeo and helped PTS America implement a Digital Asset Management Solution with workflow automation using the Nuxeo Platform.
The Solution
A Digital Asset Management solution was created by setting up a unified repository for easy storage, organization and accessibility of the graphic files. Each file had relevant metadata values added to it enabling users to easily select the search criteria they need. With the Nuxeo Platform search experience powered by Elasticsearch, the time to find and access a design was significantly brought down from a few hours, to just a few seconds. PTS America could now find designs it sometimes couldn’t in the past, and save a lot of time otherwise spent re-creating these designs.
To support working with the factory, workflows were built and PTS America has been able to get away from manually tracking the processes with spreadsheets and emails. One such workflow was built to transfer artwork to PTS’s Indonesian factory. Instead of using FTP to transfer large and bulky files, the artwork is now seamlessly loaded into Nuxeo and both teams have the same version of the files in real time. Workflows have also been designed to track the entire process from loading the artwork into the Nuxeo Platform until the factory receives it. The workflow sends notifications including when the transfer is complete and the factory acknowledges receipt of the artwork. This meant fewer emails and fewer mistakes in communicating between departments, which brought order to where there was once chaos. There are no longer issues that typically arise by two groups being out of sync with regard to file versions.
Results: Tremendous Return on Assets
Apart from saving a huge amount of time searching for designs, the Nuxeo Digital Asset Management solution helped PTS America get more value out of its assets. Designs don’t expire – they just need to wait to be trendy again. Being able to find and refer to the designs already contained in the repository and to modify them slightly to meet new requirements as opposed to having to start the design process all over again a huge time and cost saver. The ability to “not have to start all over again” is terrific.
All of this has made possible a significant cost savings and an increase in productivity. PTS America achieved at least a 20% FTE cost saving by switching to Nuxeo. Designers save around 2 hours per day that was typically spent looking for designs and managing email and spreadsheets, i.e. 10 hours per week per designer allowing PTS America designers to claim back 25% of their productivity.
Nuxeo also serves as a sales tool when it comes to presenting the designs and products to the customers. More than 10000 designs are loaded in Nuxeo so far. PTS sales teams across the organization (Europe, Asia, Americas, etc.) can now easily and quickly access designs that may interest their customers.
What’s Next
PTS America will continue to add assets in the Nuxeo repository and define more workflows. It wants to streamline the designer/buyer interaction by rolling out workflows to collaborate on design and artwork creation. The company has many other product lines, such as home furnishings, furniture, etc. which it plans to manage in Nuxeo as well.
Apart from the design process, PTS plans to roll out workflows for communicating production orders to factories, which are currently tracked using hundreds of spreadsheets. This will help smooth out the collaboration between the sales reps, the buyers, and the PTS team during the ordering process. PTS is also working on automatically feeding product data from the Nuxeo Platform into its ERP system to eliminate re-entering data and save time.
Some quotes from Charles Gallagher, Executive Vice President of PTS America:
“We haven’t found anything we couldn’t do with Nuxeo. There is work for us to do in Nuxeo for at least the next 5 years”
“Designs don’t die. It is terrific to be able to quickly pull up old designs and tweak them slightly to meet new customer requirements, and not have to start all over again”
“Once you realize the advantage of getting rid of the old practices and find this central place for collaboration, it’s irresistible”
Download Full Case Study
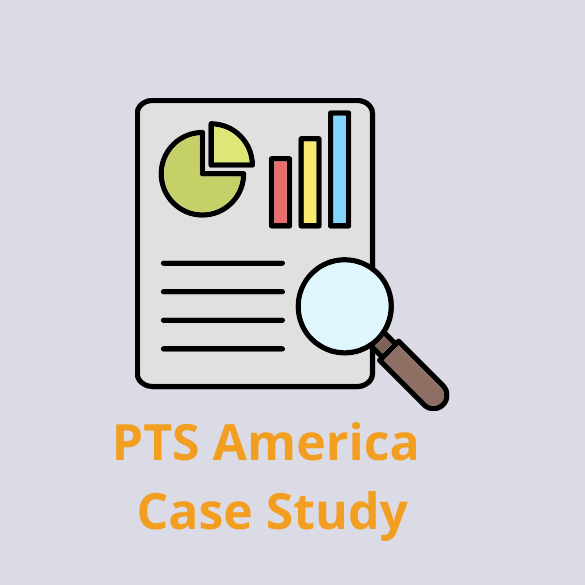
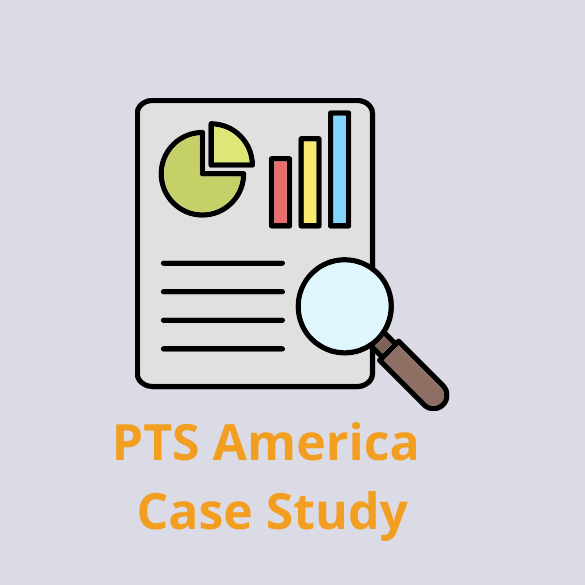